ÉCONOMIE CIRCULAIRE. Isover lance une offre de recyclage des laines de verre usagées qui permet d'éviter la mise en décharge de ces déchets de chantier et de les incorporer à nouveau, après tri et traitement, dans le process industriel. Découverte des premières étapes chez l'entreprise Excoffier Recyclage, un des partenaires de cette offre appelée à se généraliser sur le territoire.
Au moment où le gouvernement travaille à une feuille de route pour l'économie circulaire et que la question de la valorisation des déchets de la construction se pose de façon toujours plus aigüe, une filière vient de se créer pour la laine de verre. "Jusque-là, elle posait problème puisque aucune valorisation énergétique n'était possible. Comme il s'agit d'un déchet non inerte, mais non dangereux, la laine de verre est gérée par des centres de stockage des déchets ultimes de classe 2, pour un coût d'enfouissement de 100 à 150 € la tonne", annonce Valentin Lamy, directeur de site pour Excoffier Recyclage dans l'Ain. C'était sans compter sur l'opiniâtreté d'Isover à développer, pendant plus de 20 ans, une méthode de recyclage efficace. L'industriel, qui revendique la place de leader sur le marché de cet isolant avec 200.000 tonnes produites par an sur un marché français de 400.000 tonnes, a mis au point un procédé permettant de transformer ce déchet en ressource.
Isover Recycling, l'économie circulaire appliquée
Dominica Lizarazu, directrice Marketing & Développement pour Isover France, révèle : "La laine de verre est une matière recyclable à 100 % à l'infini, c'est la magie du verre". L'entreprise qui a d'abord travaillé sur les chutes propres, issues des découpes de rouleaux de ses chaînes de production, a longuement réfléchi sur l'emploi de déchets issus de chantiers de déconstruction ou de rénovation. "A l'heure actuelle entre 40 et 80 % de verre recyclé est incorporé dans la laine de verre", poursuit la spécialiste. Le site d'Orange (Vaucluse), "vaisseau amiral de la société", s'est donc doté dès 1997 d'un outil de revalorisation nommé Oxymelt qui transforme l'isolant en calcin afin de le réinjecter dans le process de fabrication de laines neuves. Ils sont fondus au moyen d'une atmosphère enrichie en oxygène qui augmente la température du four, ce qui permet d'éliminer tous les résidus indésirables dont la matière organique, nécessaire à la cohésion des fibres entre elles.
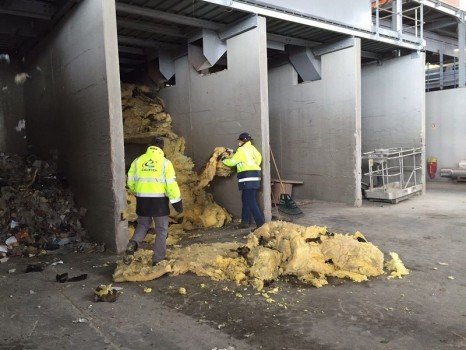
à lire aussi
Le facteur limitant, jusqu'ici, était donc la collecte de laines de verre récupérées sur les chantiers, faute de filière organisée. Isover s'est tourné vers différents partenaires spécialistes du tri des déchets et a formé des salariés pour qu'ils séparent ce produit des autres rebuts mélangés, apportés par des entreprises de curage. Une fois l'isolant visuellement inspecté et mis de côté, il est compacté dans une presse hydraulique de façon à obtenir des balles d'un poids de 400 à 800 kg, 40 fois plus denses que le matériau originel (qui emprisonne beaucoup d'air). Ces balles, qui prennent en fait la forme d'un cube d'un peu plus d'un mètre de côté, sont ensuite expédiées par camion vers Orange, pour y être fondues.
Découvrez les différentes étapes en images dans les pages suivantes