Une fois la problématique de la stabilisation de l'édifice traitée, restait à savoir comment profiter du potentiel du bois pour la production des éléments hors-site. "La standardisation des pièces permet au process d'industrialisation d'être plus rapide, et l'emboîtement des pièces les unes dans les autres permet une mise en œuvre simple sur site", explique Sidewalk labs. "Ces atouts accélèrent le processus de construction, rendent les immeubles moins coûteux et plus profitables aux constructeurs et aux gestionnaires."
Une méthode proche de celle des Lego
Sidewalk labs rapproche ces méthodes de celle des jouets Lego. "Si l'unité basique de Lego est la petite brique, pour notre projet PMX, l'unité basique est la 'cassette d'étage'." Chacune de ces pièces est faite d'un panneau en bois, incluant des couches d'isolants thermique et acoustique. Ces éléments contiennent également les réseaux, inclus dès la phase de préfabrication. Ces cassettes sont ensuite installées une par une et forment l'enveloppe du bâtiment. La société a tout mis en œuvre de manière à avoir le moins possible de cassettes différentes à produire dans un souci d'efficacité et de coût.
L'intention de Sidewalk labs est également de casser l'image de la préfabrication comme étant esthétiquement inintéressante, comme l'auraient prouvé des constructions de l'après-guerre. L'intérêt architectural peut ici provenir de la manière avec laquelle on conçoit les panneaux, "de n'importe quelle forme et matériau", à condition bien sûr qu'ils respectent la réglementation et puissent être standardisés. Pour PMX, la société a opté pour un panneau métal avec 40% de surface vitrée, accompagné d'un balcon pour chaque unité.
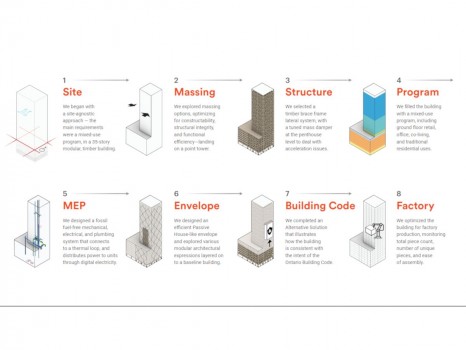
Prochaine étape, la construction de cette tour ? Quoi qu'il en soit, la combinaison de la construction bois bas carbone et du hors site aiguise l'appétit de nombreux acteurs du numérique.