SOLUTIONS ET MATERIAUX. L'isolation par projection de mousse polyuréthane sur les murs et sols est une technique encore peu développée en France. Le procédé certifié, qui permet une mise en œuvre rapide du produit, nous est expliqué par Thierry Louis, président d'Isolat France.
Pratiquée depuis 30 ans aux Etats-Unis et au Canada, l'isolation projetée polyuréthane est une technique assez peu répandue en France. Le produit, élaboré à partir de matériaux recyclés, est fabriqué directement sur le chantier et pulvérisé en une couche continue qui gonfle et se solidifie en quelques secondes. La mousse, polymère de polyol et d'isocyanate, procure alors isolation et étanchéité à l'air. "L'intérêt est de retirer le besoin d'une chape de ravoirage", nous explique Thierry Louis, président de la société Isolat France. Car la mousse se répartit sur la surface où elle est projetée, sans besoin de la préparer. "Le polyuréthane est adapté à tous les types de supports (brique, béton, pierre, bois), sauf s'il est humide ou non stable, comme le sable ou la terre", nous précise le dirigeant.
Une solution légère et durable
La couche, de 20 cm d'épaisseur, réalisée en deux passes, est rapidement solidifiée et peut ainsi être poncée afin de la rendre parfaitement plane. L'ouvrier installera ensuite une membrane permettant de placer, par-dessus, une sous-couche acoustique ou un plancher chauffant. Et la mise en œuvre, rapide, permet d'écourter le chantier : en une journée, une entreprise peut déposer entre 100 et 120 m² par jour, voire 200 m² sur les murs, l'étape de ponçage étant inutile. Le polyuréthane présenterait d'autres avantages : son poids, tout d'abord, permettrait de gagner 10 tonnes sur une maison de 100 m² grâce à l'absence de chape de ravoirage. Le matériau, qui émet une forte odeur d'urée lors de son application, ne dégage en revanche plus aucune molécule après polymérisation : il est donc classé A+ par rapport à ses émissions de COV. Quant à sa tenue au feu, "c'est un produit auto-extinguible, classé E voire M1 s'il est pulvérisé sur un support M0. Et il ne produit pas de gouttelettes incandescentes, contrairement au polystyrène, mais se transforme en poussière", ajoute Thierry Louis. Le coût de cette solution d'isolation serait même inférieur à celui d'une combinaison chape de ravoirage et isolant classique, avec un gain de l'ordre de 5 voire 10 €/m². "Au niveau des murs, l'isolant ne se tasse pas dans le temps. La solution est donc plus chère au départ, de l'ordre de 25 %, mais aussi plus définitive, ce qui est à prendre en compte. Sa durée de vie est celle de la maison", poursuit-il. Le bilan carbone serait même positif en considérant cette longue durée de vie et la totale recyclabilité du produit.
Une technologie qui a un coût
A ce jour, quatre acteurs se partagent le marché français de l'isolation projetée : Isolat, Mirbat, EuropIso et Isotrie. Ensemble, ils réalisent environ 10 % de l'isolation des logements individuels neufs, dont 4 % pour la seule société Isolat. "La maison individuelle représente 80 % de notre activité en nombre de chantiers, le reste se répartissant entre le collectif et les ERP", nous confirme le dirigeant de l'entreprise, dont l'ambition est de prendre d'autres parts de marché aux solutions d'isolation classique en doublant le nombre de chantiers d'ici à 2015. Pour y parvenir, il s'appuiera sur un réseau déjà constitué de 35 entrepreneurs concessionnaires à travers la France, qui réalisent une quarantaine de maisons par jour. Isolat a mis sur pied en 2013 un centre de formation pour ses "isolateurs" en région lyonnaise. En un an, 80 personnes, techniciens et commerciaux, ont appris à mettre en œuvre le produit. L'entreprise, qui a obtenu un avis technique du CSTB, utilise des unités mobiles de projection qui sont vérifiées par un bureau de contrôle indépendant, afin d'assurer leur bon fonctionnement. "Il faut compter 100.000 € d'investissement pour un véhicule complet", explique le chef d'entreprise.
Pour l'avenir, des travaux sont en cours pour réduire encore la taille des microcellules de la mousse, ce qui permettrait de baisser le coefficient lambda de conductivité thermique. Et de son côté, Isolat France a signé un partenariat commercial avec GDF-Suez afin de répondre ensemble aux rénovations sols, murs et combles, en proposant une solution alternative à la laine de verre dont la durée de vie est moindre. Le polyuréthane tiendra-t-il toutes ses promesses ?
Découvrez la mise en œuvre en images dans les pages suivantes.
Unité mobile de projection
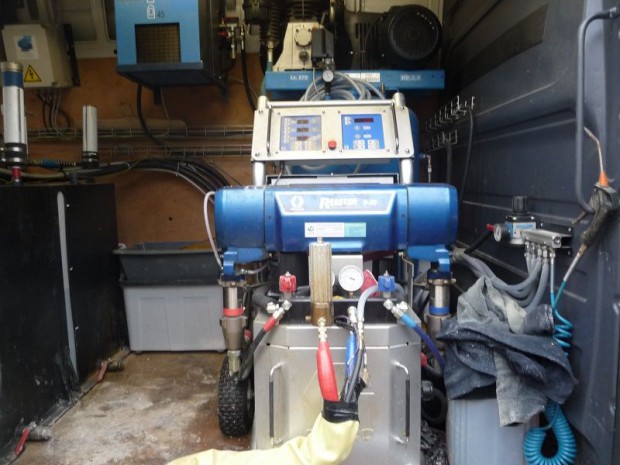
L'unité mobile de projection est contenue dans un véhicule utilitaire : à l'aide d'air comprimé et d'une résistance chauffante qui maintient le flexible à 50 °C, les deux composés (polyol et isocyanate) sont acheminés séparément au pistolet diffuseur.
Chantier
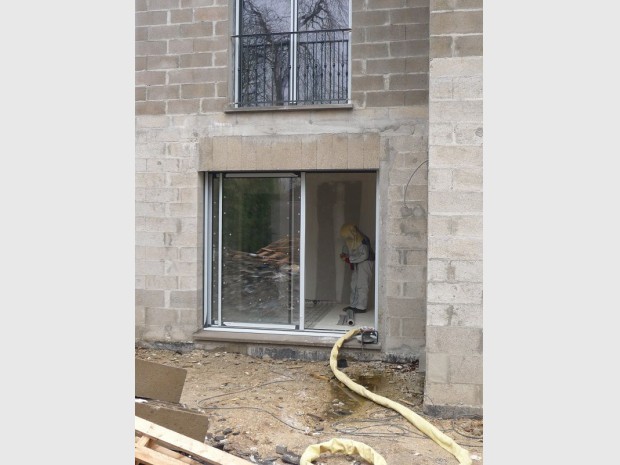
Le flexible sera manipulé par un ouvrier formé et vêtu d'une tenue de protection : la réaction chimique de polymérisation quasi-instantanée ne tolère pas d'erreur.
Projection
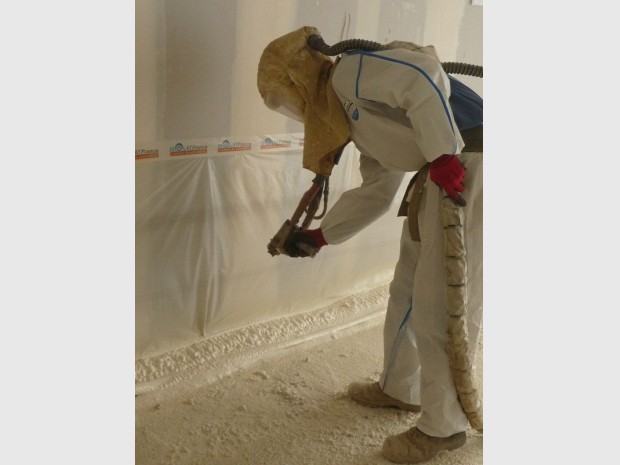
Les deux composants sont mis en contact et polymérisent. La couche déposée gonfle rapidement et se solidifie.
Résultat
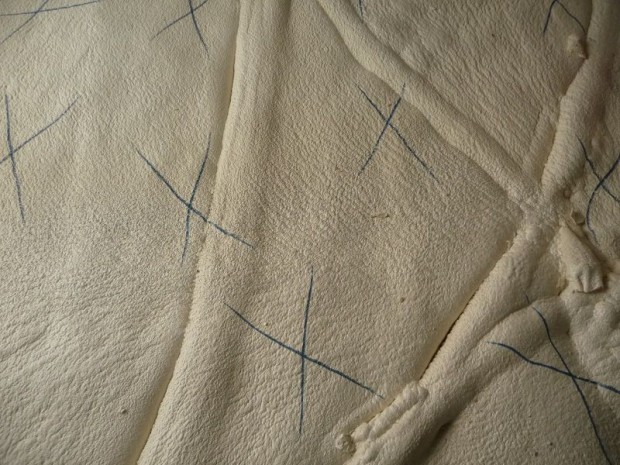
La couche se répartit uniformément sur toute les surfaces et... inégalités. Des gaines produisent donc des bosses qu'il faudra poncer afin d'aplanir le sol.
Mesure
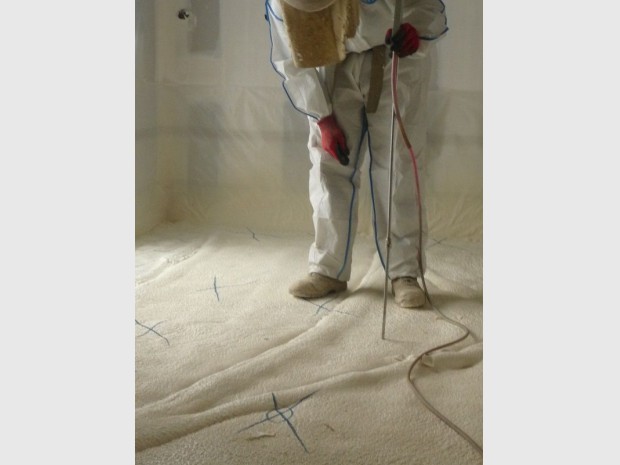
L'opérateur effectue des mesures sur la surface afin de déterminer les zones à écrêter.
Ponçage
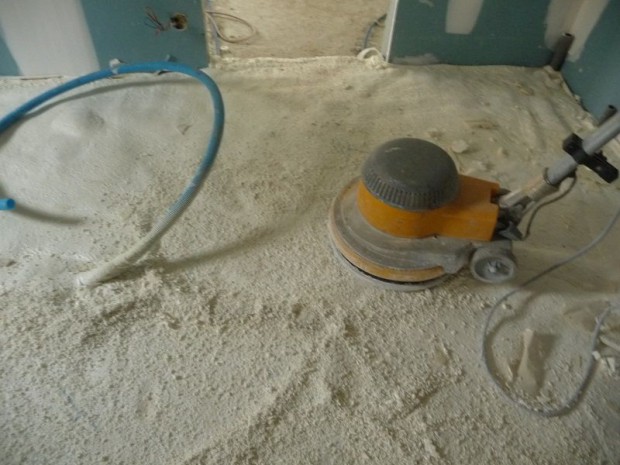
Une ponceuse est passée afin d'égaliser la surface du sol.
Finition
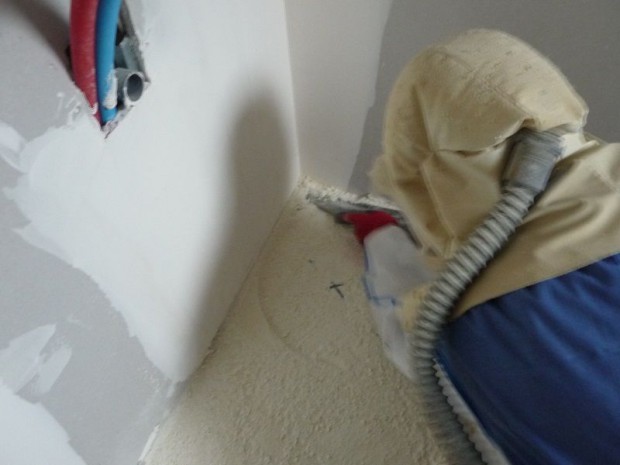
L'ouvrier inspecte la surface et termine le travail d'égalisation à la scie.
Poussière
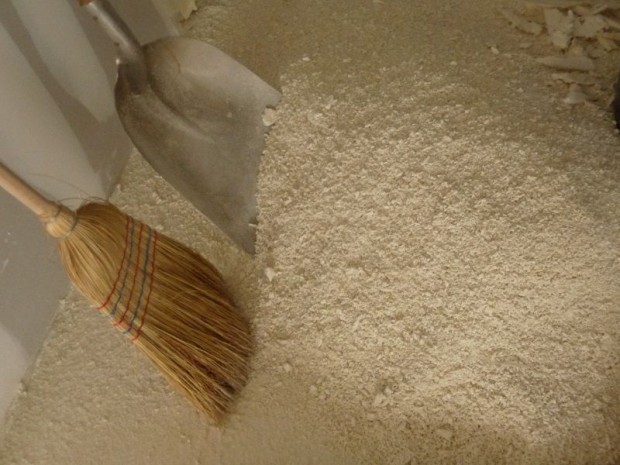
La mousse se réduit en poussière, permettant une élimination facile. Sa densité est de 2 kg/m².
Membrane
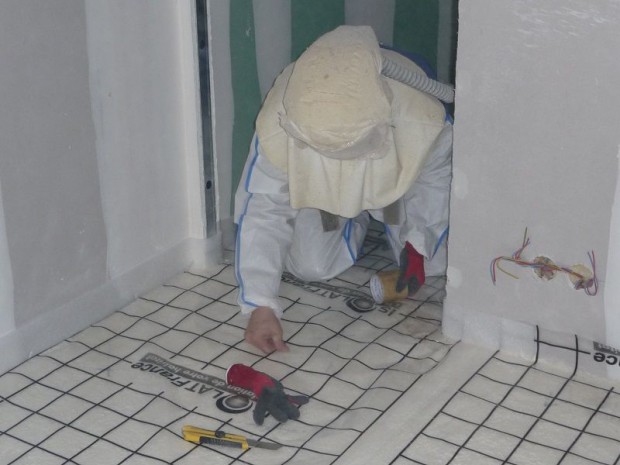
Une membrane est posée afin de séparer l'isolant du plancher chauffant qui sera posé au-dessus.