Alors que le congrès Intergalva vient de se terminer à Paris, Batiactu revient sur la galvanisation, un procédé industriel ancien qui reste compétitif. Ludovic Néel, délégué général de l'association Galvazinc, nous explique la technique et ses évolutions.
La galvanisation à chaud au trempé est une technique de sidérurgie dont les premiers brevets ont été déposés par l'ingénieur français Stanislas Sorel aux alentours de 1840. Il consiste à appliquer une couche de zinc sur des éléments fabriqués en acier (éléments de charpente ou de menuiserie). Ce traitement anticorrosion n'intervient donc qu'en toute fin de processus industriel afin de produire des pièces protégées sur toutes leurs surfaces, y compris intérieures dans le cas de formes creuses. « Il s'agit du seul procédé qui protège l'ensemble de l'élément grâce aux immersions dans des bains de traitement », précise Ludovic Néel, le délégué général de l'association Galvazinc. « Une réaction métallurgique se produit à 450 °C entre l'acier et le zinc : ils échangent des éléments et forment des composés intermétalliques qui se créent à la surface de la pièce. Ces composés sont hyper-durs, certains encore plus que l'acier, ce qui confère d'excellentes qualités de résistance aux éléments traités ». L'épaisseur du traitement n'excède cependant pas quelques dizaines de micromètres. Le traitement doit être conforme à la norme ISO 1461 (« Revêtements par galvanisation à chaud sur produits finis en fonte et en acier »), un gage de qualité qui permet à la galvanisation de se différencier d'autres procédés n'aboutissant pas au même résultat.
Aujourd'hui, une soixantaine de sites industriels de galvanisation à chaud existent en France, partageant tous le même procédé. « Ils diffèrent cependant quant aux aménagements vis-à-vis de l'environnement. Tous les sites français sont exempts de rejets, les DREAL y sont très vigilantes. Les installations comportent des bassins de rétention et des circuits de récupération des acides. Ce sont là que se focalisent les services de R&D », explique le responsable de Galvazinc. Les industriels souhaitent en effet optimiser l'utilisation des ressources dans un procédé figé. « L'autre axe de recherche porte sur la qualité et la maîtrise du process, d'un point de vue constance du produit quels que soient la nuance d'acier utilisée ou le profil de la pièce traitée. Il s'agira d'apporter des garanties de fiabilité quel que soit le site où a été réalisé le traitement ».
Durée de vie accrue pour les pièces traitées
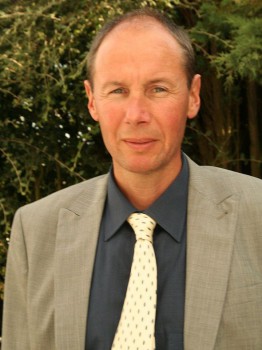
Les applications les plus courantes pour les 700.000 tonnes d'acier galvanisé produites annuellement en France sont notamment liées au bâtiment pour la réalisation de charpentes ou d'éléments de métallerie (garde-corps, etc.). Le secteur représente 40 % de la consommation totale. Mais le recours à des produits traités est généralisé : mobilier urbain (éclairage, signalisation), énergies nouvelles (supports de panneaux photovoltaïques, supports des turbines d'éoliennes marines), piscines (environnement humide particulièrement agressif contenant du chlore), usines de traitement des eaux et stations d'épuration voire matériel d'élevage (atmosphère acide). Le secteur du transport fait également appel à des pièces galvanisées, notamment pour les porte-caténaires qui doivent présenter une durée de vie supérieure à 50 ans.
Mais quel est donc le revers de la médaille ? Le surcoût initial de la galvanisation, de l'ordre de 10 %, lié au coût de la matière première qui provient principalement d'Amérique latine, de Chine ou d'Europe de l'Est. « Mais le prix global, qui prend en compte l'ensemble de la durée de vie des éléments traités, reste inférieur à celui des autres solutions », assure Ludovic Néel. La galvanisation, qui fête cette année ses 170 ans, a donc encore de beaux jours devant elle.