ÉCONOMIE CIRCULAIRE. La filière aluminium s'engage sur la voie du bas carbone avec le développement de produits recyclés, issus de menuiseries en fin de vie. Le groupe norvégien Hydro s'engage à ce que les gammes Technal et Wicona disponibles en France soient "bas carbone" à partir de 2019. Explications avec Daniel Roy (vice-président Hydro Building Systems France) et Jean-Marc Moulin (directeur du Développement durable).
La démarche de réduction de l'empreinte carbone est partout, y compris dans les menuiseries en aluminium. Ce métal, léger et inaltérable, fait des efforts pour devenir le plus vert possible. Car il part de loin : son processus de production à partir de bauxite puis d'alumine est particulièrement gourmand en énergie, qui l'associe potentiellement à des émissions de CO2. Lorsqu'elle est produite en Chine, la tonne d'aluminium dégage 20 tonnes d'équivalents CO2 ! En Europe, le recours à une électricité moins carbonée ramène cette empreinte à un peu moins de 10 tonnes par tonne de métal (environ 8,6 tonnes émises). Chez les norvégiens d'Hydro, l'approvisionnement en hydroélectricité totalement décarbonée permet d'abaisser drastiquement ce chiffre : seulement 4 tonne d'équivalent CO2 par tonne d'aluminium pour leur "Hydro 4.0" (dont 1,3 tonne de CO2 pour obtenir de l'alumine et 1,8 tonne pour la fondre). Et encore moins pour leur nouveauté, le "Hydro 75R" issu du recyclage.
à lire aussi
Daniel Roy, le vice-président d'Hydro Building Systems France, explique : "L'aluminium 75R est issu à 75 % de métal recyclé, dont des menuiseries déposées. D'où une empreinte de seulement 2 kg d'équivalent CO2 par kilogramme d'aluminium". Ce taux d'incorporation de 75 % est un minimum, car il peut dans les faits monter à 80 ou 85 % selon la qualité des rebuts utilisés. Les profilés de fenêtres sont ainsi favorisés car leur alliage 6060 est adapté. Les traces de cuivre ou d'autres métaux empêchent de monter à 100 % afin de conserver des qualités métallurgiques suffisantes. Jean-Marc Moulin, le directeur Développement durable de la division Extruded Solutions chez Hydro, renchérit : "Cette démarche s'inscrit dans l'initiative Alu+ C-. En travaillant avec le groupement des fileurs d'aluminium, nous avons souhaité développer et améliorer le recyclage en boucle fermée, profilé pour profilé". Résultat : des investissements ont été réalisés à Dormagen (Allemagne) pour collecter, trier et préparer les déchets d'aluminium avant de les expédier vers les fours de l'unité de Clervaux (Luxembourg) où ils sont fondus et ajoutés à une fraction de métal neuf. Grâce à ce procédé, la firme norvégienne dépasse largement l'engagement d'aluminium "bas carbone" fixé à 6,7 tonnes d'équivalent CO2 par tonne de matériau.
L'intégralité de la production de 75R destinée à la France
La production de la petite usine de Dormagen, capable de retraiter environ 36.000 tonnes par an, sera intégralement réservée à la fabrication de gammes Wicona et Technal destinées au seul marché français, éléments de façade et menuiseries à partir du mois de juin 2019. Des fiches environnementales européennes "EPD" spécifiques à Hydro seront publiées dès le mois de mars, tandis que des FDES françaises seront éditées plus tardivement. Grâce à ces avancées techniques et organisationnelles, le groupe norvégien assure faire chuter le bilan carbone d'une fenêtre, qui passe ainsi de 500 kg (pour une fenêtre double battant à double vitrage) à seulement un peu plus de 200 kg, soit l'équivalent d'une menuiserie PVC elle aussi recyclée. Une empreinte allégée qui permettra de répondre plus facilement à la future réglementation environnementale des bâtiments, attendue pour 2020. D'autant que la durée de vie des menuiseries en aluminium est considérée comme plus longue que celle des produits en PVC.
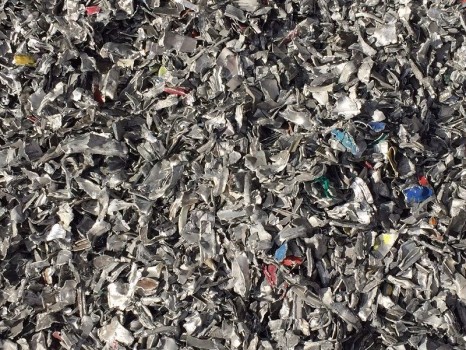
Techniquement, le 75R est obtenu par collecte de déchets de déconstruction de bâtiments, de préférence en circuit court, afin de limiter les transports. Les profilés sont broyés et déchiquetés, puis séparés en différentes fractions par élimination des éléments en fer ou en acier (aimants), tamisés, puis soumis à un courant de Foucault (pour discriminer l'aluminium des autres métaux) et enfin passés au rayons X, cette fois pour ne conserver que les éléments d'une densité adéquate. Les copeaux obtenus sont ensuite fondus pour obtenir de l'aluminium. La quantité d'énergie nécessaire s'avère beaucoup moins élevée que celle requise pour produire du métal neuf. Convaincu du procédé développé, Hydro a d'ores et déjà initié la construction d'une autre unité de recyclage en Espagne cette fois.
à lire aussi
L'aluminium pèsera lourd dans la transition
Les déchets d'aluminium sont ainsi largement valorisés et réemployés dans le bâtiment pour une deuxième vie. Les spécialistes estiment que 95 % du métal utilisé dans les constructions est aujourd'hui récupéré, seuls 5 % finissant en décharge. L'enjeu sera de réduire encore cette fraction pour parvenir à du 100 % de recyclage. Ou presque, car les rendements ne sont jamais de 1 pour 1 et les pertes sont inévitables. Mais grâce aux efforts entrepris par la filière aluminium, le matériau se positionne comme solution adaptée aux enjeux de développement durable et d'économie des ressources naturelles. Hydro dispose ainsi de 30 fonderies dans le monde (douze en Europe) pour une capacité de 2 millions de tonnes d'aluminium dont 150.000 tonnes de rebuts remis dans la boucle. La firme, qui émet 15 millions de tonnes de CO2 par an, vise pourtant la neutralité carbone dès 2020 par différentes mesures de réduction de l'empreinte globale, de développement de solutions plus efficaces, de recyclage poussé et de responsabilisation lors de l'extraction. Une chasse au carbone facilitée par l'intégration verticale du groupe qui dispose de mine de bauxite (au Brésil) et d'unités de transformation largement alimentées par de l'électricité propre (70 % de renouvelables). Il faut noter que, dans ses calculs, le géant norvégien intègre les bénéfices apportés par l'aluminium chez ses clients, notamment la capacité de produire des véhicules plus légers et donc moins gourmands en carburant : pour 100 kg économisés sur la balance, une voiture émet 8 grammes de CO2 de moins pour chaque kilomètre parcouru. Les vertus de l'aluminium pèsent lourd, en définitif.